Introduction
Definition of veneered MDF - MDF panels with a thin veneer layer on surface Manufacturing Process
Veneered medium-density fiberboard (MDF) is an engineered wood product constructed by applying a thin layer of decorative wood veneer to one or both faces of MDF panels. MDF itself is made by breaking down hard and soft woods into wood fibers, which are then combined with resin binders and pressed into sturdy panels under high temperature and pressure. The resulting MDF boards consist of densely packed wood fibers with a uniform smooth surface devoid of grains or knots. A veneer made from thin slices of wood no more than 1/32 inch thick is then firmly bonded to the core MDF during a secondary lamination process. Common veneer species include oak, maple, cherry, birch, and exotic hardwoods. Adding a natural wood veneer layer allows the MDF boards to take on the aesthetic qualities of solid wood, revealing an attractive wood grain pattern and rich coloration. Veneered MDF matches the dazzling visual appeal of all-wood counterparts at a fraction of the price. The veneer face can be clear-finished, painted, or stained to achieve different looks for furniture, cabinetry, architectural millwork and other end-uses where the appearance of real wood is desired without the cost.
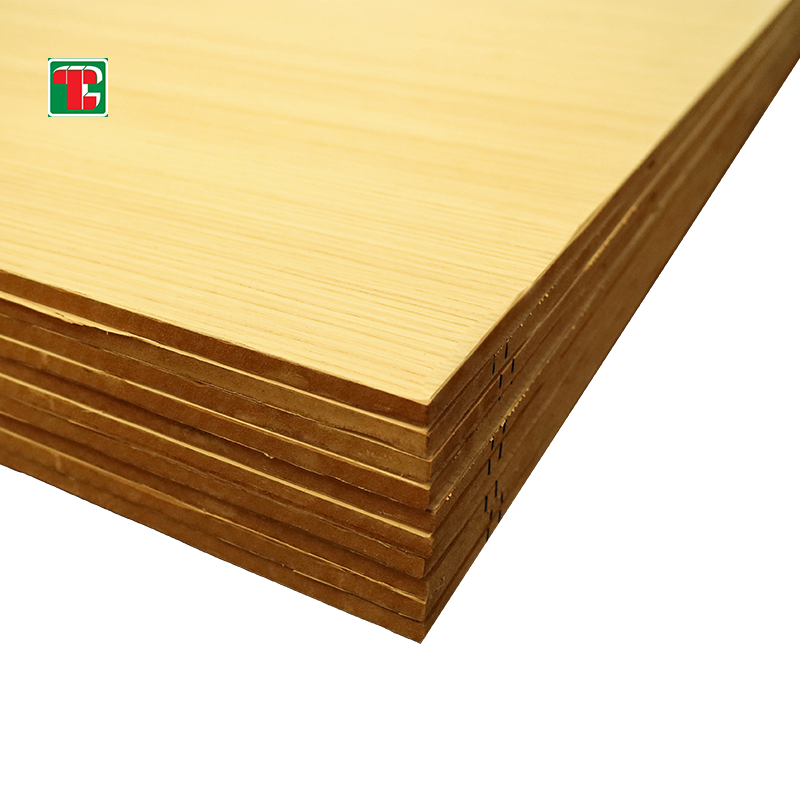
MDF sheets constructed by bonding wood fibers using resin
The base material of veneered MDF starts as MDF panels that are fabricated by breaking down harvested wood sources into fibers through a defibering process involving mechanical grinding, crushing, or refining. The individual wood fibers are then blended with bonding agents containing urea-formaldehyde or other resin adhesives. The mixed resin and wood fibers then go through a process of pre-compression and molding to form a loosely shaped mat laid out in a panel configuration. The resin-saturated mats then undergo final high heat and high pressure compression in a hot press machine to densify and set the adhesive bonds between fibers. The resulting medium-density fiberboard emerges with a multi-layered cross-oriented fiber matrix consolidated into a uniform, void-free rigid panel. These base MDF boards have consistent physical properties but lack an aesthetic wood grain pattern on the surface. To add decorative appeal, veneers harvested from rotary-peeled logs or sliced logs are adhered to one or both MDF panel faces using adhesives.
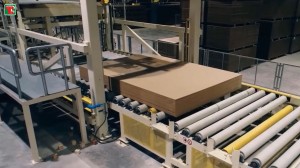
0.5mm veneer coating applied on each side
The veneer wood sheet applied to MDF panels is approximately 0.5 mm (or 0.020 inches) thick, equivalent to 1/32 of an inch, making it paper-thin yet able to reveal an attractive grain pattern on the surface through transparency.
Edges left exposed or edge banding applied
With veneered MDF, the panel edges are either left exposed with the brown MDF core visible, or edge banding strips made from PVC/melamine are applied during finishing to fully encase the panels and achieve clean, aesthetic edges that match the veneer surfaces.
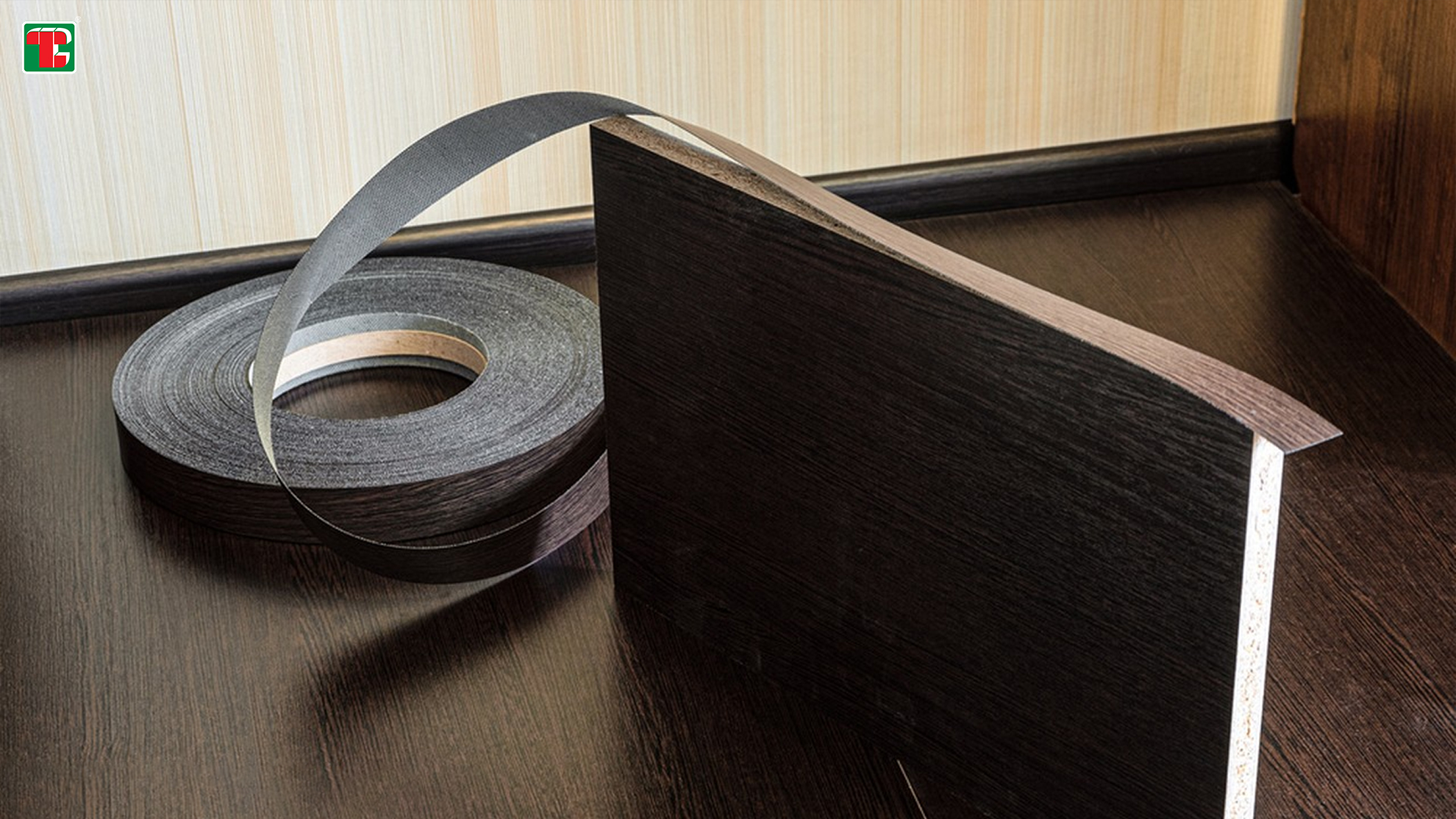
Types of Veneered MDF
Overview of wood veneer varieties (oak, teak, cherry)
Veneered MDF takes advantage of a vast array of wood veneer options to provide decorative and aesthetic surfaces. Some of the most popular wood veneers applied to MDF cores include oak, teak, cherry, maple, birch, ash, and mahogany. Oak veneer is valued for its strong, bold grain patterns and timeless beauty. Teak veneers impart a luxurious golden brown color and exotic look. Cherry veneers reveal an elegant, reddish-brown tone. Maple veneers create a clean, bright blonde-toned appearance. These natural wood veneers showcase unique grains, textures, and colors from sustainably harvested tree species that enhance the look of mundane MDF substrates. Additional stain and finish processes further expand the stylistic possibilities of various wood veneers on MDF panels
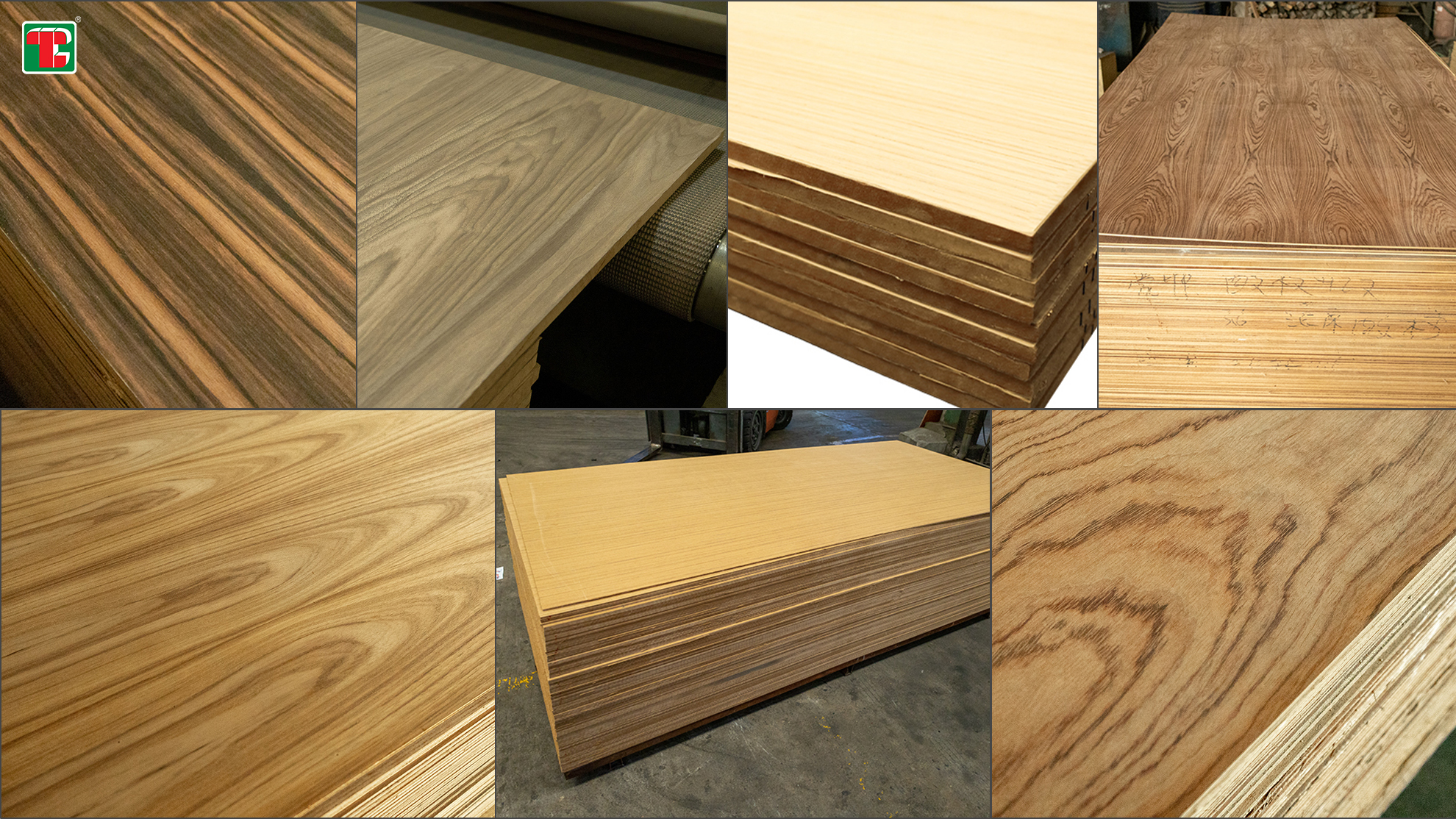
Sheet sizes and thickness options
Veneered MDF sheets are primarily manufactured in dimensions of 4x8 feet (1220mm x 2440mm) and 5x10 feet (1525mm x 3050mm) as full untrimmed panels. Common panel thickness options include: 6mm (0.25 inches), 9mm (0.35 inches), 12mm (0.5 inches), 16mm (0.625 inches), 18mm (0.75 inches) and 25mm (1 inch). Custom sheet sizes and thicknesses outside these general standards can also be specially ordered. The panels can be further fabricated with secondary cutting and machining into specific rectangular dimensions, shapes, and molded profiles as required. Veneered MDF offers flexibility in sheet goods formats to suit the specifications of various casework, furniture, architectural millwork, and other end-use design needs.
Visual characteristics of each veneer type
The natural beauty of wood veneers lends unique visual flair to veneered MDF panels. Oak veneers showcase prominent grain patterns with distinctive arching wood rays. Cherry veneers reveal smooth, fine, straight grains marked by a rich reddish-brown complexion. Maple veneers demonstrate uniformly blonde tones and gently flowing wave-like parallel grains without much figuring. Walnut veneers offer an elegant mosaic grain mix of chocolate brown and creamy tan hues. Rosewood veneers impart a distinctive coarse grain texture punctuated by dark streaks on a ruddy orange-brown backdrop. The color variations, wood figures, and graining visible in each wood veneer type infuse ordinary MDF substrates with appealing aesthetic qualities reminiscent of solid lumber.
Applications and Uses
With its attractive woodgrain surfaces, consistency, and affordability, veneered MDF is widely utilized for manufacturing furniture pieces including beds, tables, cabinets, shelves, and display units for residential and commercial spaces. Veneered MDF also lending itself well to architectural millwork such as wainscoting, ceiling treatments, door skins, crowns & base moldings. The material is also popularly used throughout the fixtures and displays in retail stores, restaurants, offices, hotels and other commercial establishments. Additionally, veneered MDF serves as a versatile product for cabinet carcasses, office systems, laminated panels, signage backings, and exhibits & event construction where both appearance and structural integrity are important. Industries from hospitality to education to healthcare all leverage veneered MDF as a reliable substrate supporting beautiful wood veneer facades.
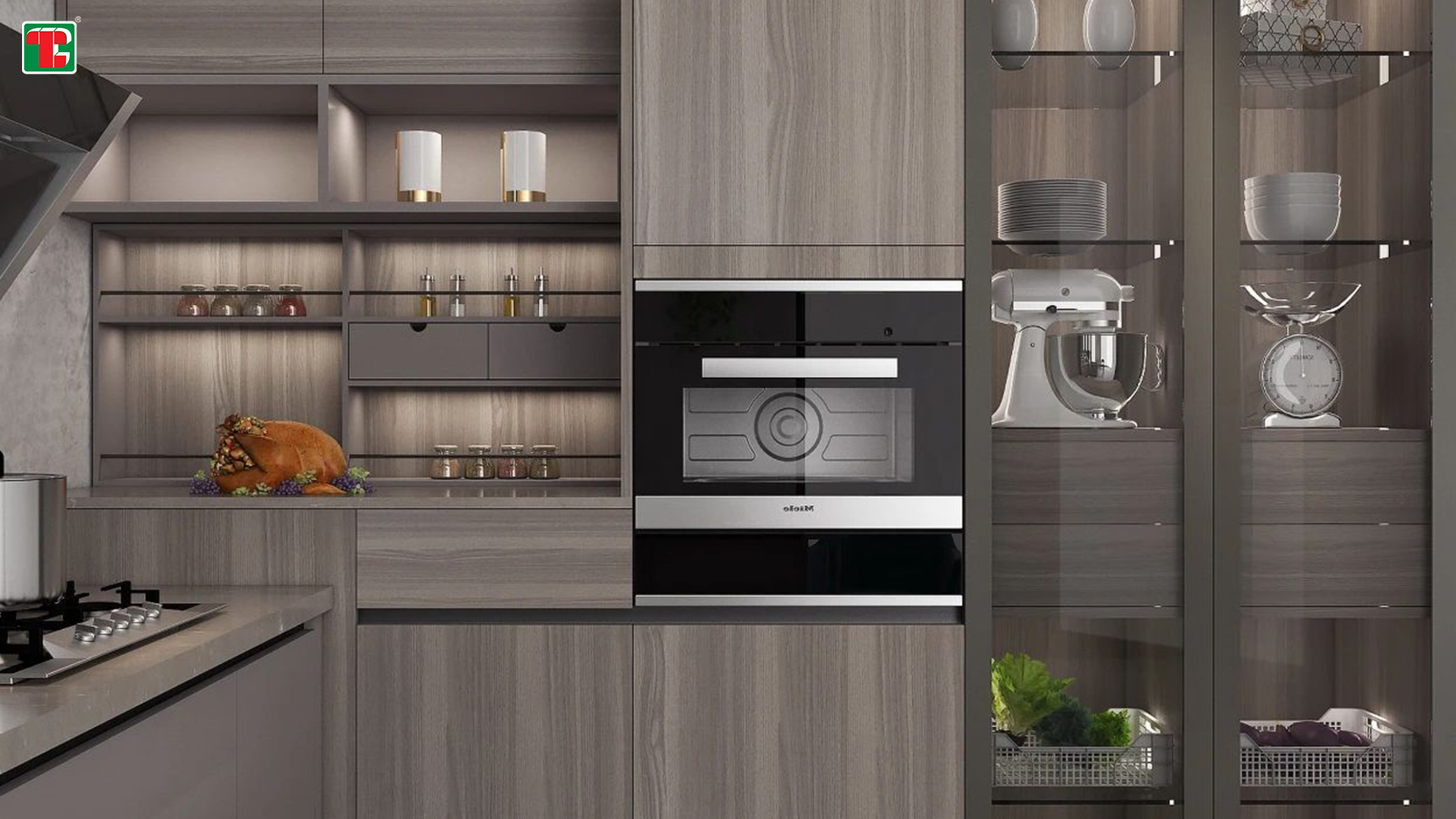
Comparisons to Solid Wood
More affordable than solid wood
A major advantage of veneered MDF is that it provides the aesthetic woodgrain pattern and richness of solid lumber at a fraction of the cost, given the high-yield efficiency of wood fiber utilization in MDF manufacturing and the thin veneer layer requiring less raw material.
Offers similar decorative grains and textures
With its thin wood veneer layer, veneered MDF replicates the natural beauty of decorative grains, figures, and textures found in traditional solid wood materials at a comparable level of aesthetic quality and appeal.

Pros and cons of using veneered MDF
Veneered MDF provides several major benefits including cost savings, structural reliability, and decorative versatility. The composite panels are cheaper than solid wood, less prone to warping, and offer customizeable veneer surface options. However, veneered MDF also comes with some disadvantages. The panels are heavier than solid wood and do not allow for intricate carvings. Moisture protection requires extra diligence as water can lead to swelling issues over time if not properly sealed. Screws and fixtures must be installed carefully to avoid cracking the brittle veneer layer. Overall though, the pros generally are perceived to outweigh the cons, making veneered MDF a continually popular choice as an affordable, decorative wood product able to substitute for solid lumber across residential and commercial settings when properly understood and implemented.
Post time: Mar-01-2024