Plywood, an engineered wood product, stands as a versatile material widely utilized in the many country for various construction projects. This comprehensive guide delves into its composition, benefits, drawbacks, types, grading, applications, properties, pricing, cutting techniques, safety considerations, and decorative options.
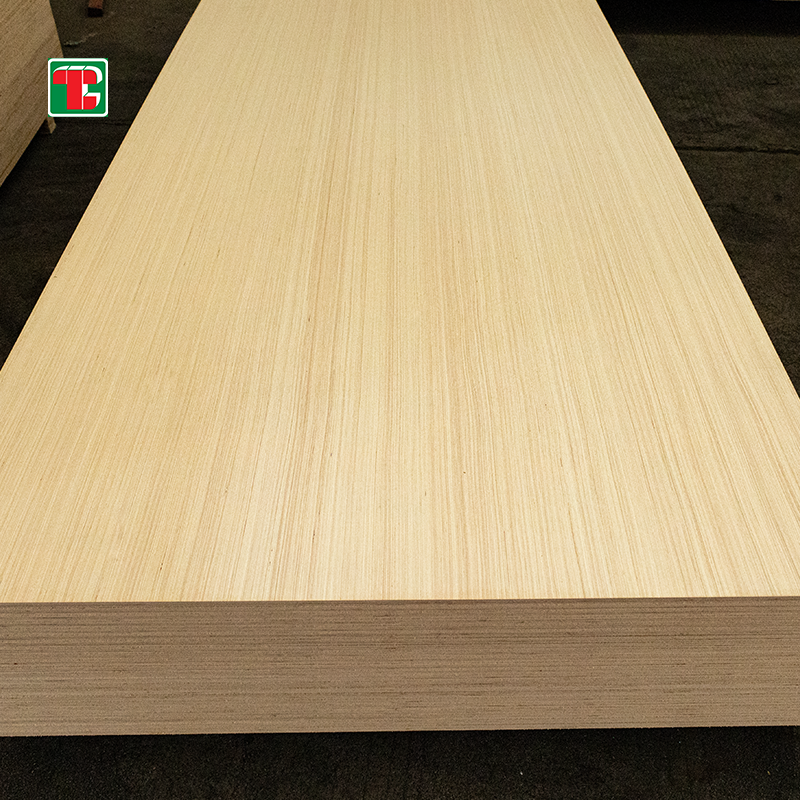
1.Plywood Definition and Composition:
Plywood, a stalwart in construction and woodworking, is an engineered wood product crafted from layers of veneer. These veneers, thin sheets of wood, undergo a meticulous bonding process using resin adhesive, culminating in a composite material known for its versatility and strength.
Composition:
The magic of plywood lies in its layered structure. Multiple sheets of veneer are strategically arranged, and each layer's grain direction is rotated by 90 degrees relative to its adjacent layers. This ingenious cross-lamination technique contributes to the material's robustness, enhancing its resistance to bending forces.
Resin Adhesive and Curing:
The layers of veneer are bound together using a resilient resin adhesive, often of the phenol-formaldehyde variety. This adhesive, known for its water-resistant properties, ensures a durable bond between the layers. The composite assembly then undergoes a curing process, subjecting it to elevated temperatures and pressure. This process solidifies the layers into a unified panel, ready to tackle a myriad of applications.
Outer Veneers:
A distinguishing feature of plywood is the differentiation between face veneers and core veneers. Face veneers, typically of a higher grade, serve both functional and aesthetic purposes. Not only do they contribute to the overall strength, but they also provide a smoother and more appealing surface, making plywood suitable for a range of finishes.
Purpose of Core Layers:
Within the layered core, the primary function is to increase separation between the outer veneers. This strategic placement is designed to counteract bending stresses, augmenting the material's resistance to external forces. The core layers play a pivotal role in plywood's ability to withstand various structural challenges.
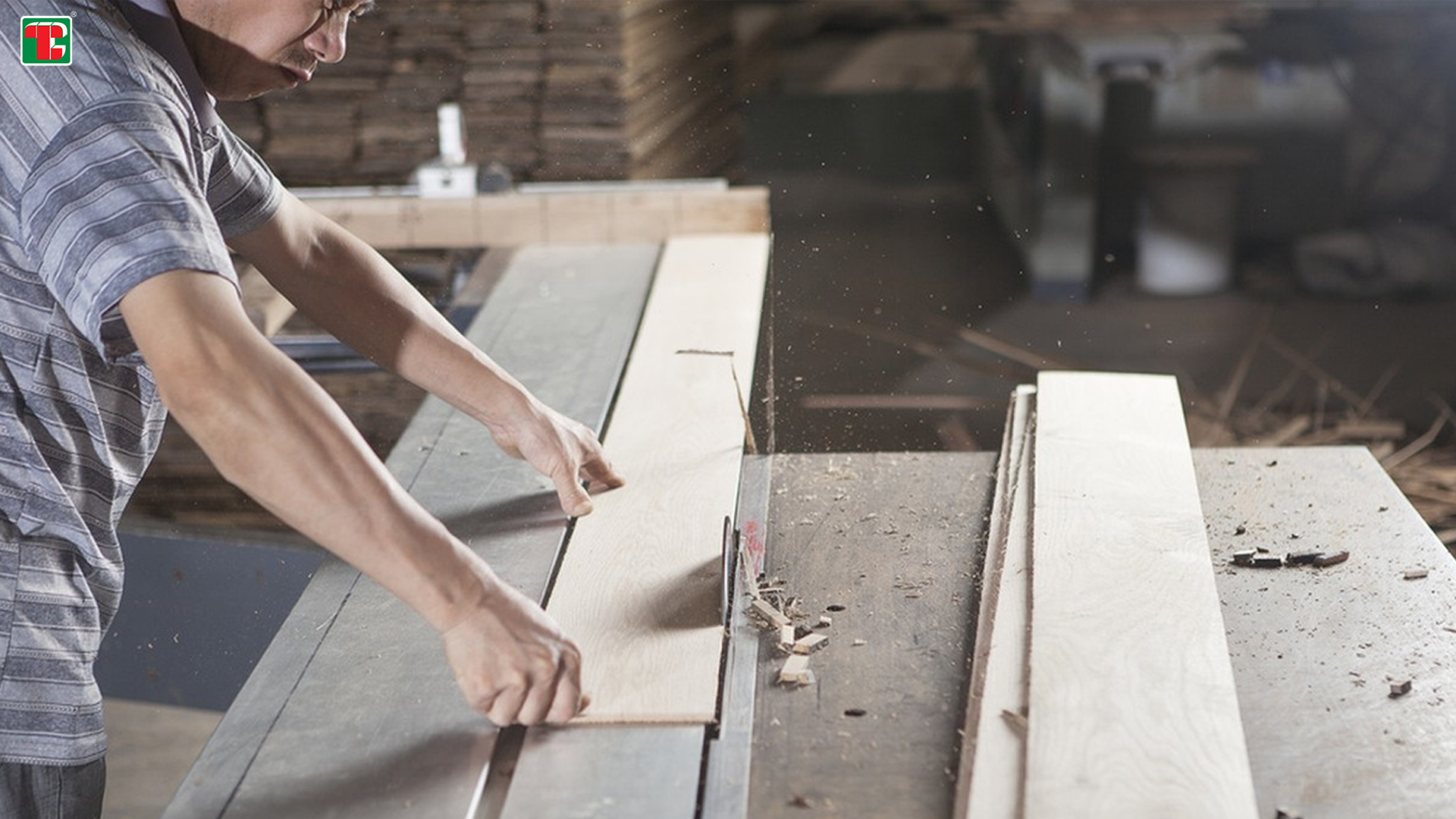
2.Benefits of Plywood
Plywood, a versatile engineered wood product, has become a staple in construction and woodworking, offering a plethora of advantages that cater to both professionals and DIY enthusiasts.
(1) Diverse Sizes and Thicknesses:
Plywood's adaptability shines through its availability in a wide range of sizes and thicknesses. This characteristic makes it a go-to material for diverse construction projects, allowing for flexibility and customization.
(2) Exceptional Strength:
Among engineered woods, plywood stands out as one of the strongest. While it may not match the graded strength of timber, its construction, with adjacent layers of real wood, imparts remarkable sturdiness. This strength makes plywood a preferred choice for applications demanding robust performance.
(3) Variety of Types:
The market offers an array of plywood grades and types tailored to specific needs. This diversity empowers users to select products aligned with the requirements of their projects, showcasing the material's adaptability and broad applicability.
(4) Ease of Nail and Screw Application:
Plywood's structural integrity and veneer composition make it conducive to secure nailing and screwing. It holds fasteners effectively, minimizing issues related to splitting—an advantage that sets it apart from other engineered wood alternatives.
(5) Bendability:
Certain plywood types exhibit a remarkable flexibility, allowing for bending. This feature proves invaluable in the construction of both small and large structures, such as ramps and curved elements, adding a dynamic dimension to plywood's utility
(6) Lightweight Advantage:
In the realm of construction, weight is a critical consideration. Plywood excels in this aspect, offering a relatively low weight compared to its counterparts. This characteristic eases handling and contributes to its popularity in various applications.
(7) Cost-Effectiveness:
Plywood emerges as an economical choice in construction materials, presenting a cost-effective alternative to traditional timber. Its affordability has been a driving force behind its widespread adoption in both professional and DIY projects.
3. Drawbacks of Plywood
While plywood stands as a versatile and widely-used engineered wood product, it's essential to acknowledge and navigate its drawbacks. These considerations provide a holistic perspective for builders, designers, and enthusiasts working with this material.
(1) Surface Decoration Challenges:
Plywood's rough texture poses a challenge when it comes to surface decoration. Sanding down plywood may result in issues such as splintering and chipping layers, making it less ideal for certain aesthetic applications compared to smoother alternatives like MDF.
(2) Vulnerability to Moisture:
In its standard form, plywood is susceptible to moisture absorption over time. This can lead to swelling, changes in shape, and potential damage to the bonds between veneers. While there are moisture-resistant options available, it's crucial to choose the right type of plywood for applications exposed to damp conditions.
(3)Emissions During Cutting:
The adhesives used in plywood can release potentially harmful gases when the material is cut. Proper precautions, including cutting in well-ventilated areas and using protective gear like gas masks and safety goggles, are necessary to mitigate any health risks. Thoroughly cleaning surfaces after cutting is also advised.
(4) Difficulty in Sawing:
Plywood's layered structure can result in challenges during the sawing process, leading to rough edges and splintering. Using specific tools and techniques tailored for cutting plywood panels is essential to achieve clean cuts. This complexity in comparison to easily cut materials like MDF adds a layer of consideration for those working with plywood.
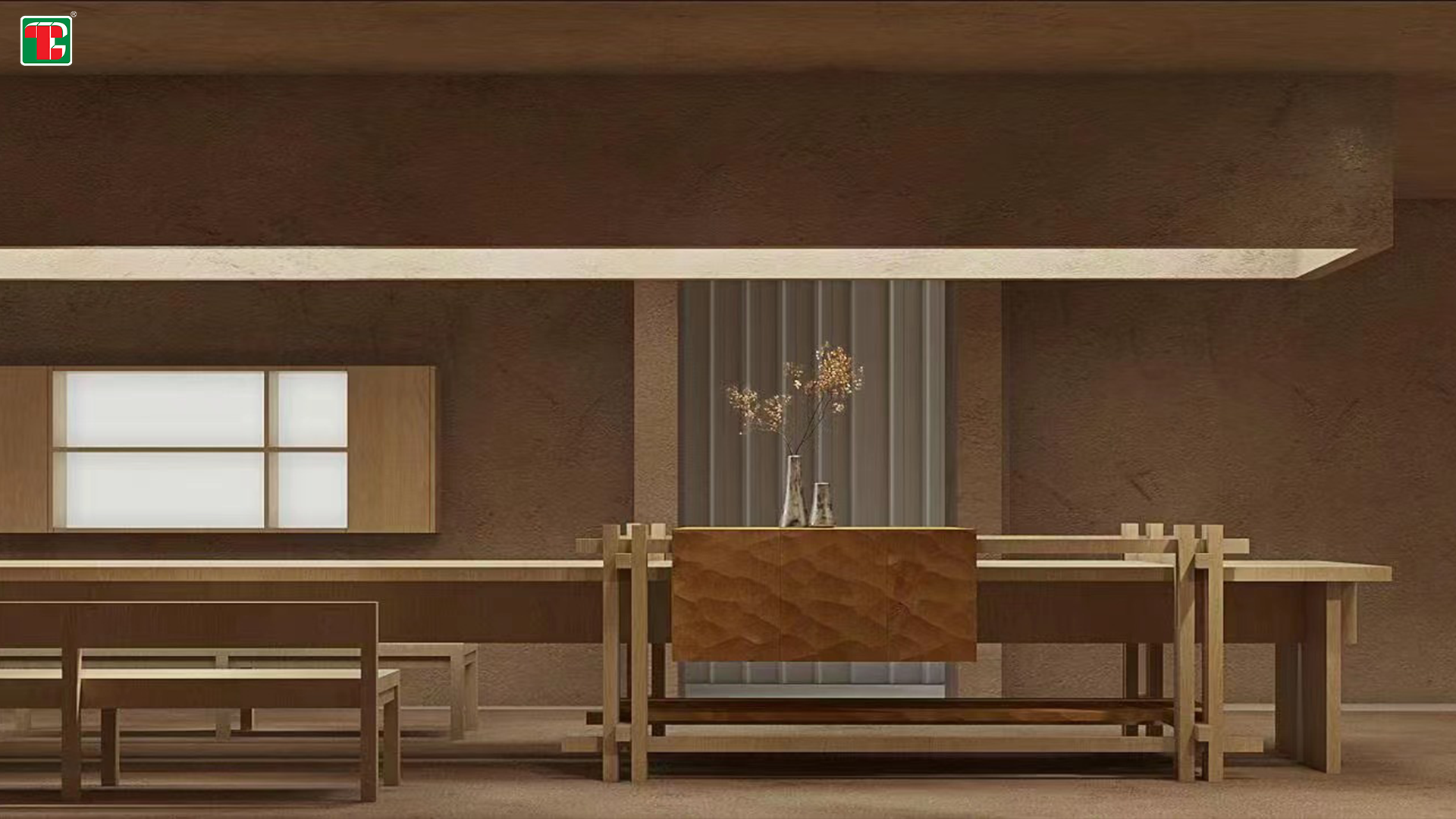
4.Types of Plywood
Plywood, a versatile engineered wood product, boasts an array of types tailored to diverse applications. Understanding these variations is pivotal for selecting the right plywood to meet specific project requirements. Here's a comprehensive guide to the types of plywood and their respective applications:
(1) Structural Plywood:
Composition: Bonded with strong adhesives for enhanced strength and durability.
Application: Ideal for structural uses in buildings, providing robust support and stability.
(2) Marine Plywood:
Composition: Crafted with waterproof glue for resistance to moisture and water.
Application: Well-suited for external applications, boat construction, and any project exposed to high humidity.
(3) Flexible Plywood:
Composition: Designed for flexibility, achieved by aligning the grain of each veneer.
Application: Perfect for curved applications, offering a clean and adaptable solution for various design needs.
(4) Softwood Plywood:
Composition: Faced with softwood veneers (e.g., cedar, douglas fir, pine).
Application: Commonly used in building and formwork applications, typically not chosen for its visual appearance.
(5) Hardwood Plywood:
Composition: Features hardwood veneers, providing greater strength.
Application: Suited for heavy-duty uses, furniture, paneling, and even instrument-making.
(6) Insulated Plywood:
Composition: Includes an insulated foam core between two plywood layers.
Application: Ideal for structurally insulated panels (SIPs) in homes, providing insulation for walls, ceilings, and floors.
(7) Shuttering Plywood:
Composition: An economical option used for temporary construction needs.
Application: Commonly employed as formwork for concrete pours or to cover broken windows temporarily.
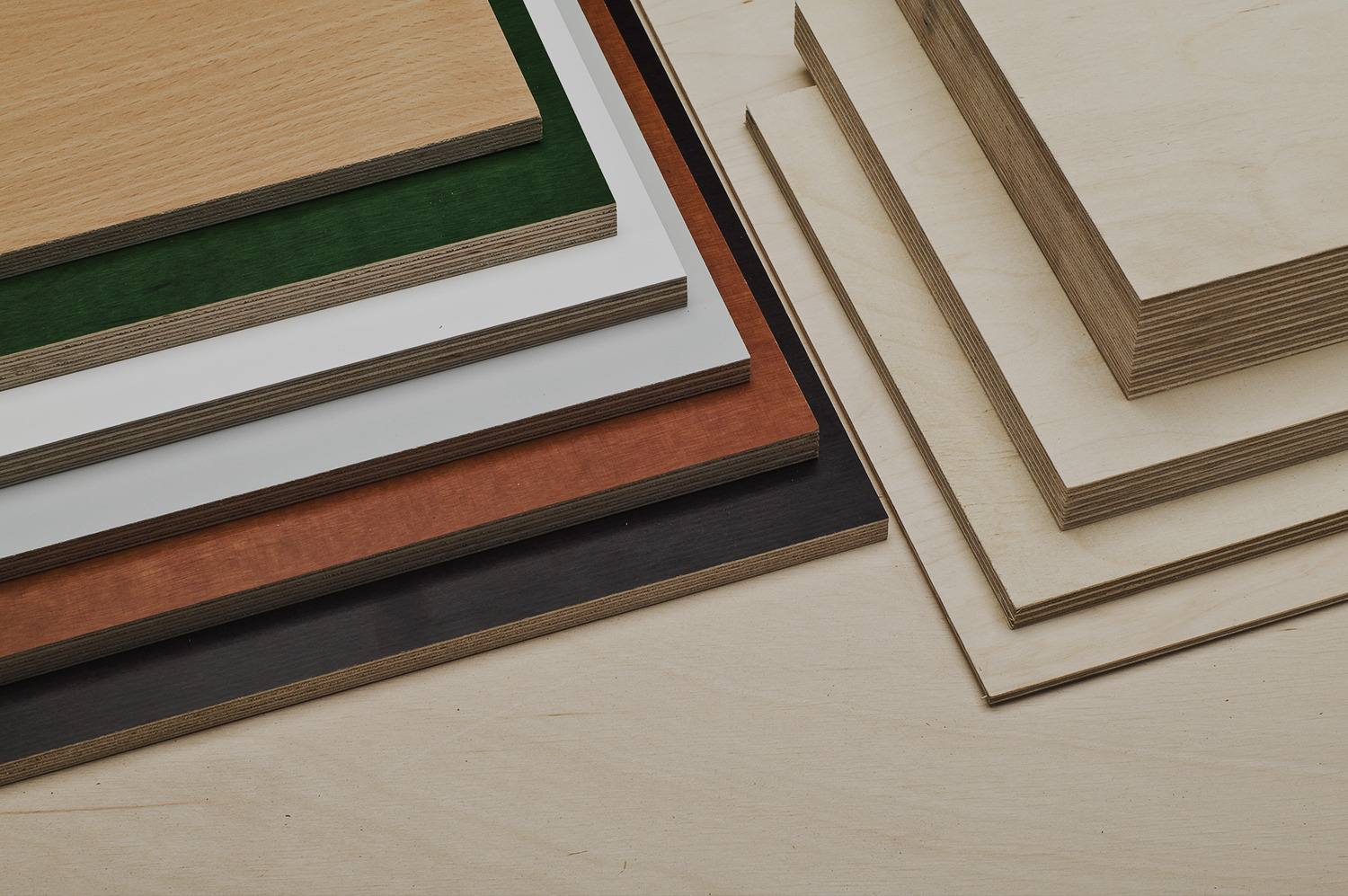
5.Grading of Plywood
Class I: Suitable for dry interior use.
Class II: Suited for humid interior environments and occasional water contact (e.g., kitchens, bathrooms).
Class III: Designed for exterior use and frequent water contact.
Visual Grading Options:
Plywood also comes with visual grading options, allowing users to choose based on aesthetic or structural considerations:
AB Grade: Consistent surface with small pin knots.
B Grade: Less consistent with changes in color and wood grain.
BR Veneer Grade: Similar to B grade but with smaller knots.
BB Grade: Allows larger knots, suitable for non-aesthetic uses.
C Grade: Used for strength-based applications, may have visible discoloration, splits, and knots.
CC Grade: Splits, open knots, and discoloration, used for non-visual applications.
6.Uses of Plywood in Building Projects
Plywood, an engineered wood product renowned for its strength and adaptability, plays a pivotal role in a myriad of building projects. From structural elements to aesthetic finishes, plywood finds applications across various domains within the construction industry. Here's a detailed exploration of how plywood is utilized in building projects:
(1) Furniture:
Application: Plywood's strength and appealing grain make it a preferred material for crafting a range of furniture items.
Examples: Tables, chairs, storage units, display cases, bedframes, and more.
(2) Roofing:
Application: Plywood serves as roof decking or sheathing, providing a sturdy base for shingles.
Benefits: The strength of plywood is advantageous for roofing applications, and its superior water resistance compared to alternatives like MDF mitigates risks of dampness.
(3) Flooring:
Underlay: Plywood is traditionally used as an underlay for flooring materials like carpet, laminate, or hardwood.
Affordable Flooring: Plywood can also serve as a cost-effective standalone flooring material when cut to size and installed.
Considerations: Opting for water-resistant plywood may be necessary depending on the room's moisture levels.
(4) Wall Framing:
Application: Plywood can be used for both covered and exposed wall framing, offering durability and natural acoustic properties.
Options: Stained high-grade plywood sheets for a modern look or structural plywood as a cladding base for other wall coverings.
(5) Boats and Docks:
Marine Plywood: Specifically designed for water-resistant properties, marine plywood is a common choice for boat construction.
Docks: Plywood, especially marine-grade, offers a cost-effective and low-maintenance solution for dock construction.
(6) Exterior Projects:
Application: Plywood is employed in various exterior applications, such as facades and outdoor structures.
Considerations: Marine plywood or other water-resistant options may be preferred for prolonged exposure to the elements.
(7) Decorative Paneling:
Application: Plywood, especially high-grade variants, can be used for decorative paneling in both residential and commercial spaces.
Finishing Options: Staining or painting plywood allows for customization to match the desired aesthetic.
(8) Insulation:
Insulated Plywood: Structurally insulated panels (SIPs) with insulated plywood cores provide an effective solution for insulating walls, ceilings, and floors.
(9)Shuttering and Temporary Uses:
Shuttering Plywood: Economical and suitable for temporary needs like covering broken windows or as formwork for concrete pours.
7.Used For Within a Building Project
Plywood is used throughout both the construction and furniture industries when a quality engineered wood is called for. The different gradings and types available offer further benefits within a variety of applications.
(1) Furniture
The strength and attractive grain of quality plywood allows it to be used to make an array of quality furniture items. Everything from tables, chairs, storage units, display cases, and bedframes can be produced from sheets of plywood. You can also use sheets of plywood with moisture-resistant properties, such as marine plywood, to construct external furniture items like doghouses.
(2) Roofing
Roof decking, sometimes called sheathing, is the underside of your roof that is connected to your house, on which the shingles will be hung. The strength of plywood makes it a great choice, and its superior water performance compared to other engineered woods like MDF will also benefit due to the risks of dampness within a roof. As this is a non-visible use, you can use a lower grade model, with knots and splits, though strength should still be prioritised.
(3) Flooring
Plywood has traditionally been used as an underlay for other flooring materials, but it can also be used as an affordable flooring by itself. For an underlay, you’ll be looking to use interlocking plywood sheets to create a steady base, onto which carpeting, laminate, or authentic hardwood can be fitted. For the flooring itself, plywood boards with a high visual grading can be cut to size and easily installed like traditional floorboards. This will be more cost-effective than traditional hardwood flooring, but the downside is that plywood gets scratched more easily. Depending on the room you’re installing your plywood flooring in, you may also need to opt for a water-resistant option.
(4) Wall Framing
Plywood can be used as a wall framing, and can be covered or left exposed, much like a floor. Plywood offers good durability and natural acoustic properties. Stained high-grade plywood sheets can be cut to size and used for a sleek modern look, or alternatively structural plywood can be used as a cladding base for other wall coverings. For wall framing, using fire-resistant plywood can be beneficial, slowing the progression of flames in the event of a fire.
(5) Boats and Docks
While it has other uses in exterior locations or areas at high moisture risk, marine plywood is named as such due to its common use in boats and docks. Due to its resistance to rot and moisture, marine plywood is popularly used in boat construction. It’s worth bearing in mind that any boat made with marine plywood will need to be sealed before it is seaworthy. Marine plywood is also used as a cost-effective and low-maintenance choice for docks, due to its quality performance in the water.
8.Plywood Properties
Plywood, a versatile and widely used engineered wood product, boasts a range of properties that contribute to its popularity in various construction applications. Understanding these properties is essential for informed decision-making in selecting plywood for specific projects. Here's a comprehensive exploration of the key properties of plywood:
(1) Composition:
Definition: Plywood is composed of multiple layers of veneer, thin sheets of wood, bonded together with resin adhesive.
Layer Arrangement: Layers are positioned with the grain at a 90-degree rotation on each layer, enhancing strength.
(2) Strength:
Comparative Strength: While not surpassing graded timber, plywood ranks among the strongest engineered woods.
Construction Basis: Strength is derived from the adjacent layers of real wood in its construction.
(3) Sizes and Thicknesses:
Versatility: Plywood can be manufactured in a wide variety of sizes and thicknesses, catering to diverse building project requirements.
(4) Types and Grades:
Structural Plywood: Meets specific standards for strength and durability, crucial for strength-based applications.
Marine Plywood: Designed with water-resistant properties, suitable for external applications and boat construction.
Flexible Plywood: Engineered for easy bending, catering to curved applications in construction.
Softwood and Hardwood Plywood: Differ in wood veneer composition, with hardwood offering greater strength for heavy-duty uses.
Insulated Plywood: Features an insulated foam core between plywood layers, providing structural soundness and insulation.
Shuttering Plywood: Economical and used for temporary construction needs.
(5) Moisture Resistance:
Considerations: While some types are moisture-resistant, most plywood absorbs moisture over time, potentially causing damage.
(6)Fire Resistance:
Combustibility: Regular plywood is combustible, but fire-resistant options, treated with fire-retardant chemicals, slow the spread of fire.
(7) Grading:
Moisture Performance: Graded into classes indicating suitability for dry interior use, humid interiors, or exterior applications.
Visual Grading: Options like AB for consistent surface to CC for non-visual applications, allowing tailored selections.|
(8)Weight:
Comparative Lightness: Plywood is lighter than some competing engineered wood products, enhancing its suitability for construction.
(9) Cost:
Affordability: Plywood is a cost-effective building material compared to traditional timber, contributing to its widespread use.
(10) Sustainability:
Sourcing: Sustainability is contingent on responsibly sourced wood; plywood, when sourced sustainably, has a comparatively low environmental impact.
9. Cutting and Safety
Cutting plywood demands precision and safety precautions to achieve clean, professional results. Here's an insightful guide on cutting plywood efficiently while prioritizing safety:
(1) Tools and Blades:
Selection: Choose blades specifically tailored for plywood to minimize tearing.
Sharpness: Ensure tools are sharp to reduce the risk of tearing and achieve cleaner cuts.
(2) Safety Precautions:
Ventilation: Cut plywood in a well-ventilated space to mitigate the release of dangerous dust from adhesives.
Protective Gear: Wear full safety gear, including a gas mask and safety goggles, to shield against potentially harmful dust.
(3) Cutting Techniques:
Table Saw: Ideal for straight cuts, a table saw equipped with a plywood blade ensures precision.
Circular Saw: Efficient for various cuts, a circular saw with a suitable blade is versatile and easy to maneuver.
Hand Saw: Use a hand saw for smaller projects, employing controlled, steady strokes for smoother edges.
(4) Personal Safety:
Ventilation Space: If possible, cut plywood outdoors to minimize indoor dust accumulation.
Cleaning: Thoroughly clean and vacuum all surfaces after cutting to eliminate residual dust.
(5) Special Considerations:
Fire Resistance: Be cautious when cutting fire-resistant plywood, as certain chemicals used may pose additional safety concerns.
Precision: Maintain precision in measurements and cuts to avoid wastage and ensure pieces fit seamlessly.
(6) Decorative Finishing:
High-Grade Plywood: Higher-grade plywood is suitable for visual applications, allowing for finishes like painting and staining.
Sanding: Sand plywood before finishing to create a smooth surface, reducing the risk of splintering.
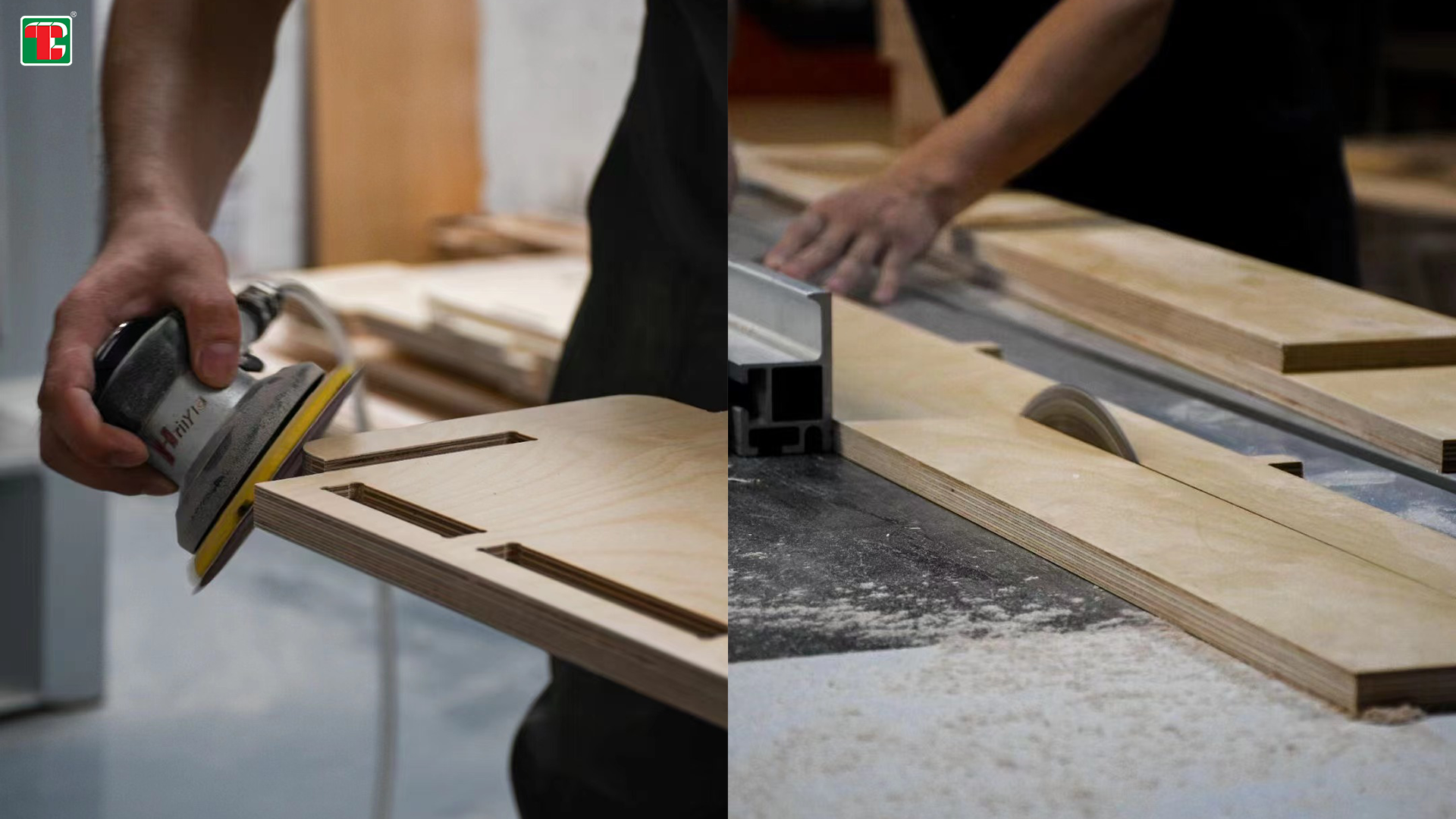
10. Will plywood mold or rot?
The susceptibility of plywood to mold or rot depends on its exposure to moisture. In its standard form, plywood is not inherently resistant to prolonged exposure to water, and it can be prone to mold and rot if consistently damp or wet. Here are some key considerations:
(1) Moisture Resistance:
Regular Plywood: Standard or untreated plywood is not designed to be waterproof, and it can absorb moisture over time, leading to swelling, warping, and eventually mold and rot.
Water-Resistant Options: There are water-resistant plywood options available that are treated with special chemicals or coatings to provide increased resistance to moisture. Marine plywood, for example, is designed for external use and has water-resistant properties.
(2) Preventive Measures:
Sealing: If using standard plywood in areas prone to moisture, it's advisable to seal the wood with an appropriate sealant to minimize water absorption.
Varnishing or Painting: Applying a waterproof varnish or paint to the plywood surface can create a protective barrier, reducing the risk of moisture penetration.
(3) Ventilation:
Proper Ventilation: Ensuring proper ventilation in areas where plywood is used can help prevent the accumulation of moisture and mitigate the risk of mold and rot.
(4) Specialized Plywood:
Marine Plywood: Marine plywood, designed for use in marine environments, is made with waterproof glue and is less prone to mold or rot. It is a suitable choice for applications where the wood will be exposed to water.
(5) Storage and Installation:
Dry Storage: Plywood should be stored in a dry environment to prevent moisture absorption before installation.
Proper Installation: Plywood should be installed with proper spacing and ventilation to allow for natural drying and minimize the risk of trapping moisture.
In conclusion, plywood emerges as a go-to material in construction and furniture industries, offering a myriad of benefits and applications. Understanding its types, grading, properties, and considerations for cutting and decorating provides a holistic view, empowering professionals and DIY enthusiasts alike in making informed choices. As plywood continues to evolve, staying informed about innovations and trends becomes crucial for anyone engaged in construction projects.
Post time: Nov-22-2023